GE Renewable Energy is Hiring | Engineer, Lean & CI |
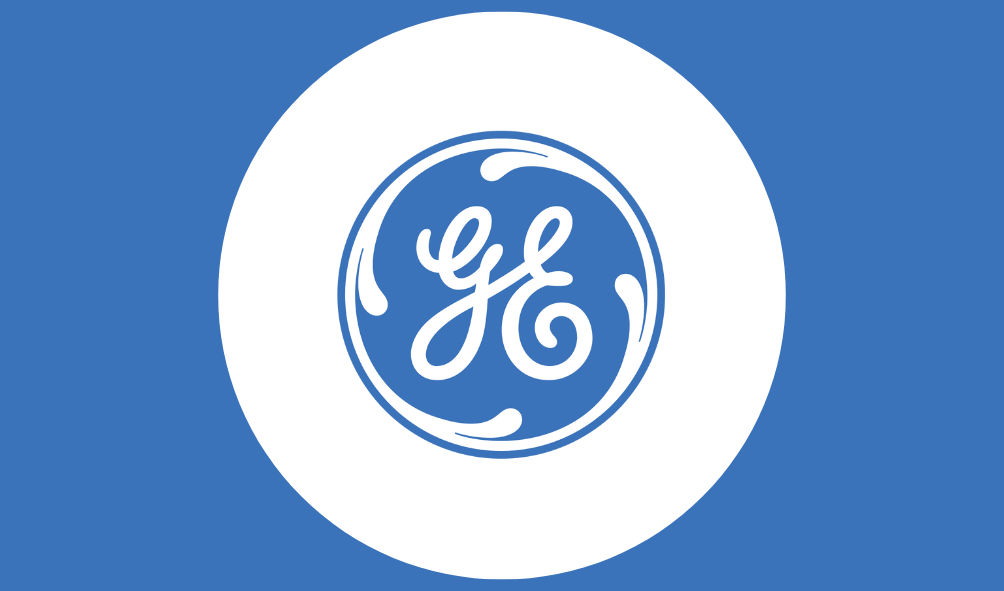
Position – Engineer, Lean & CI
Company – GE Renewable Energy
Location – Bengaluru, Karnataka, IN
Job description
Job Description Summary
Process and quality improvement roles Impact the quality of own work and the work of others on the team. Executes standard operational/technical tasks typically subject to instructions and work routines. There is latitude to rearrange the sequence to complete tasks/duties based on changing work situations.
Job Description
Roles and Responsibilities
- An active supporter of plant Lean strategy
- Coordinate & prioritization of Lean activities
- Inform about Lean KPI´s status
- PLM to coach/ guide & support Lean Coordinators/KPOs
- Highlight key points/priorities/risks and support/resources needed
- To guide & support module owners with LMPS implementation.
- To promote Lean culture on the shop floor and identify improvements
- Drive and/or support Lean improvement initiatives
- To Coach/ guide local team on Lean standards and methods
- Support, and provide standards and methods
- Share best practices to be communicated globally by Lean official channels (eg. Newsletter, intranet, BP global meetings, etc.)
- Provide updates on ongoing & performed activities including financial and non-financial impact.
- Get support for financial improvement calculation
- Work with Lean analytics to ensure numbers a validated
- Support/deliver Lean Strategy in the Plant
- Influence key stakeholders of Lean Strategy
- Develop/support Lean culture through activities and behaviors
- Ensure plant has Lean capacity and capability versus standards, continually enhance Lean skills, and practices across the plant
- Ensure Lean teams are focusing on improving their main KPIs
- Ensure the plant follows agreed LM/GE Lean standards
- Ensure relevant plant communication on Lean improvements through the defined channels
- Support/conduct relevant assessments (e.g. LMPS, LEAN/BF)
- Lead/Support on small to medium-level impact projects (mainly PDCA or GB projects)
- Follow-up projects (time, impact, sustainability)
- Facilitate execution and when necessary provide additional coaching and training
- Support/run plant Action-Work-Outs (AWOs)
- Where necessary provide full project life cycle support
- Track the financial impact of initiatives
- Communicate the status of results of projects to relevant stakeholders
- Coordinate Why-Not via standard processes through to sustainable execution
- Identify from Why-Not? Program Best Practices for sharing and implementing
- Lead and drive LMPS at the plant
- Support on plant LMPS road map Development
- Implementation of LMPS across plant
- Track implementation at the plant
- Best practice sharing
- Feedback loop to GLL: Processes and Methods
- Define and execute /support the LMPS training plan at all levels and areas (link also with CoE)
- Support training, development processes
- Support evaluation & feedback
- Coach & mentor team members and stakeholders
- Fully engage with the ‘Share Beliefs’ culture
Required Qualifications
- Minimum of a Bachelor’s degree with a strong preference in Industrial, Mechanical, Electrical, Chemical, or Manufacturing Eng. required (from a recognized Institute)
- 0-4 years of experience across the value chain of which 2 years were dedicated to Operations
Desired Characteristics
- Strong verbal and written communication skills. Ability to document, plan, market, and execute programs.
[su_button url=”https://jobs.gecareers.com/global/en/job/R3734464/Engineer-Lean-CI” target=”blank” background=”#0274be” size=”6″ center=”yes” radius=”5″ icon=”icon: share-square-o” text_shadow=”0px 0px 0px #0274be” desc=”*You will be redirected to company website.” id=”Apply now”]Apply Now[/su_button]