TATA Motors is Hiring | Multiple Openings |
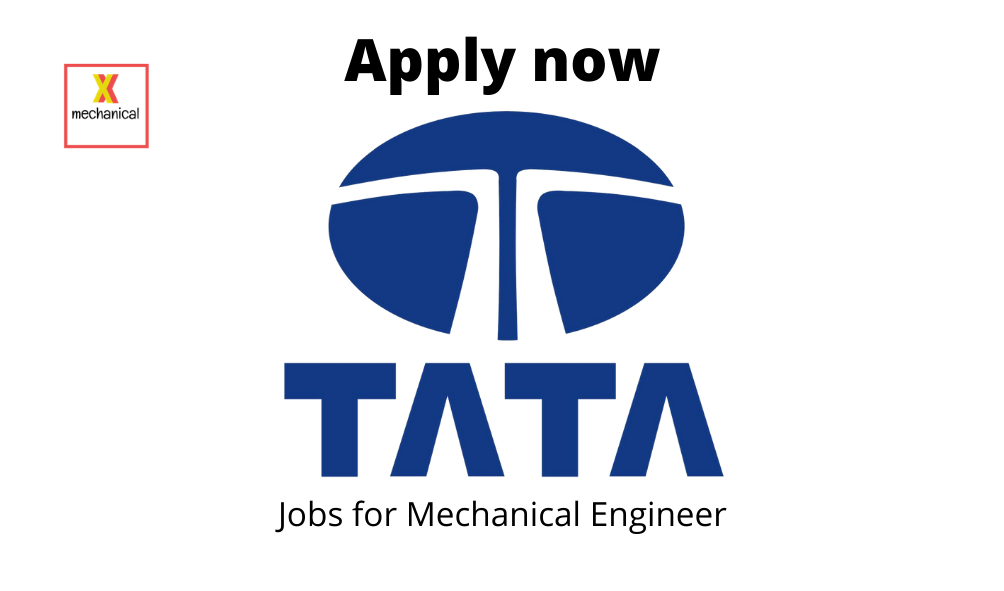
Position – PFT PRODUCTION
Company – TATA Motors
Location – Maharashtra, IN
Job description
Position Summary with Job Responsibilities
Personal Profile
Education Diploma (Mechanical/Elec./EnTC/Production)
Skills/ Competencies
- Customer Centricity
- Leading Change
- Operations Management
- Problem solving orientation.
- Risk management
Relevant Experience :
- Must possess overall experience of 0-3 years in the Shop technology, and must possess sound technical knowledge
Key Responsibilities:
- Production Planning
- Prepare and arrange for tools and equipment required for the production, as per the defined production plan
- Follow up with Warehousing to ensure the availability of raw materials for the planned production mix
- HPeV
- MOP
- JPH
- New Product Development
- Drive compliance to station level readiness, against the 120-point checklist provided by the Technical Services
- Make arrangements for all relevant machines and equipment for the testing of new products
- Provide inputs to Technical Services regarding specific issues faced at the line and create a detailed action report for course correction • Station readiness – 95%
- Process Quality Improvement
- Execute the action plan, prepared basis the feedback received from internal and external customers
- Report line issues for improvement in production • PQI Score (Process Quality Index)
- TCF DPV(Defect /Veh) Score
- Productivity Improvement
- Take actions to eliminate NVA (non-value adding), and ENVA through line balancing and various initiatives (Kaizen, Kaizen events, FPBP etc.)
- Try out various initiatives identified for line functionality improvements
- Coordinate with shop logistics/indirect material stores for availability of indirect material and tools to ensure maximum productivity • % Down Time improvement (YOY)
- HPeV
Education
Work Experience: Work experience continued-
5 Manpower Management
- Train operators on specific line skills and soft skills (MS Office, MES System etc)
- Coordinate with SQPDCME and HR to ensure training compliance of the Operator staff • Manpower requirement
- Training compliance
6. Shop Health Management
- Provide TPM trainings to operators and reinforcing the same in culture
- Participate in ICR/ICM- cross functional teams to identify new steps to keep cost levels minimum
- % of Improvement (Rejection, warranty ,IDM and Tool Cost) YOY
7 Safety Management
- Drive acceptance and usage of Safety PPE’s among Operators and temporary blue collar and ensure minimum Safety incidents
- Arrange for the PPEs on the shop floor
- TRCFR
- Safety audit score
8 Cost Management
- Provide inputs for preparation of annual Shop production budget basis of the production requirement
- Execute initiatives to derive value from waste
- Track and control Rejection, Indirect Material and Tools cost by proactively planning and executing initiatives
- Annual maintenance budget
9 Other initiatives
- Execute actions for reduction of costs through TCS (Transportation, Consolidation, Services)
- Achieve WCQ Targets
- Cost/per car
- VAVE
- Level
Tata Motors Leadership Competencies
- Customer Centricity – Anticipating, understanding and focusing efforts on meeting the customer (stakeholders) needs or expectations
- Developing Self and Others – Recognizing continuous development is essential for success and taking steps to develop self and helping others to excel
- Driving Execution – Translating strategy into action and execution
- Leading by Example – Encouraging and following ethical standards
- Leading Change – Recognizing the need for change, initiating and adapting to change
- Motivating Self and Others – Inspiring teams and individuals
Position – SENIOR MANAGER (L5)- TCF SHOP
Company – TATA Motors
Location – Maharashtra, IN
Job description
Position Summary with Job Responsibilities
- To Plan, Coordinate and Supervise successful execution of Assembly Line activity in TCF/Vehicle Assembly Shop.
Education
- B.E. / B.Tech – Mechanical Engineering / Automobile Engineering
Work Experience
- Exp- 3 to 5 Years
SKILLS :
- Good knowledge about the vehicle assembly process
- Knowledge about IATF, TQM, TPM, OHSAS18001.
- Knowledge about PFMEA ,SPC and M-PPAP and HIRA.
- Proficiency in MS Office.
- Ability to maintain shop floor in good condition.
- Strong analytical skill & technical Problem solving capability
- Understanding & interpreting fitment / Part drawing.
- Knowledge about aggregates & its function.
- Demonstrating high level of skill in functional area.
- Should have expertise in PDCA, SDCA & DWM. [TQM]
- Knowledge about WCQ and Standardized work will be an added advantage.
- Knowledge about Line balancing, VA/NVA analysis.
Tata Motors Leadership Competencies
- Customer Centricity – Anticipating, understanding and focusing efforts on meeting the customer (stakeholders) needs or expectations
- Developing Self and Others – Recognizing continuous development is essential for success and taking steps to develop self and helping others to excel
- Driving Execution – Translating strategy into action and execution
- Leading by Example – Encouraging and following ethical standards
- Leading Change – Recognizing the need for change, initiating and adapting to change
- Motivating Self and Others – Inspiring teams and individuals
Position – SENIOR MANAGER -BRAKE DESIGN_VSE
Company – TATA motors
Location – Maharashtra, IN
Job description
Position Summary with Job Responsibilities
Position Name: Vehicle Systems Engg. (Chassis)
Location (City/Region) Pune (M.H)
BU: BU Engineering (CV)
Function: Vehicle Systems Engg. (Chassis)
Hiring Manager Name/Function/location: Mahesh Shridhare
Role Reports to ((Designation – Role of reporting manager): L3(GM)
BHR: ARCHANA SARAF
Band & Level: Level 5
Brief Role Description (one line description including travel if any) 3 to 10 years for graduate engineer or Postgraduate Engineer in Mechanical / Automobile.
Working experience in Pro/E (preferred), PLM (preferred) of 2 to 5 years.
Education
Work Experience
Job roles & responsibilities:
- Knowledge of brake system or Automobile chassis component its application with exposure to design guidelines and calculations.
- Design proposal, 3D modelling, 2D drawings & aggregate packaging in ProE (PTC) Creo with exposure to GD&T.
- Design optimization and validation through interaction with CAE team.
- BOM Preparation and complete design group release in PLM with adherence to timeline
- Conducting DFMEA, DFS,DFM and DFA signoff activity with CFT team
- Supplier and IDT interaction for component level development and validation.
- Co-ordination for prototype build and support for Vehicle testing.
- Regular co-ordination with production, vehicle integration, service and supplier team for production issue resolution.
- Should be able to optimize the process of release, change management and project documentation for design review.
- Should be ready to work in Shifts
Functional/Technical
- Well versed with mechanical design of components & knowledge of brake system
- Should be expert in Pro – E software of Pro Engineering
- Knowledge of release process in PLM.
- Essential & Desirable Education/Qualifications/ Work experience/technical skills i.e. what are the ‘must haves’ for this role
- Education , Skills & Experience
- Must have Graduate or Post-graduate in Mechanical or Automobile Engineering(Good to have)
Tata Motors Leadership Competencies
- Customer Centricity – Anticipating, understanding and focusing efforts on meeting the customer (stakeholders) needs or expectations
- Developing Self and Others – Recognizing continuous development is essential for success and taking steps to develop self and helping others to excel
- Driving Execution – Translating strategy into action and execution
- Leading by Example – Encouraging and following ethical standards
- Leading Change – Recognizing the need for change, initiating and adapting to change
- Motivating Self and Others – Inspiring teams and individuals
Position – SENIOR MANAGER (L5)- WAREHOUSING & PACKAGING SOURCING
Company – TATA motors
Location – Gujarat, IN
Job description
Position Summary with Job Responsibilities
Purpose of the position
- The role will be responsible for managing warehouse operations by supplying uninterrupted supply of right quality of material to manufacturing with optimum resources within TML and /or from Service Providers by complying to Safety, regulatory requirements and company policies.
Dimensions of the position
Non-financial:
Personal Profile
Education B.E./B. Tech (Mechanical/Elec.)
Skills/ Competencies
- Driving Execution
- Customer Centricity
- Leading Change
- Operations Management
- Business and financial acumen
- Problem solving orientation.
- Risk management
Relevant Experience :
- Must possess overall experience of 4-8 years in the Supply Chain management, and must possess sound technical knowledge of Warehousing Operations of minimum 2 years
Key Responsibilities:
S.N. Key Responsibility & Key Tasks Measures
- Warehousing operations management
- Prepare shop wise plan and execute inbound material receipt, its safe storage and issue as per production plan
- Ensure availability of material at right consumption point and escalate non-availability of material as per MIN MAX levels in order to ensure uptime of production levels
- Drive Smooth Material flow from receiving to point of use
- Adhere to JIS/JIT/Kanban methodologies for lean inventory management
Education
Bachelor of Engineering in Mechanical
Diploma – Other in Supply Chain
Work Experience
- Prepare shop wise layout and material flow solutions for optimisation of regular / new project material as per WCQ standard (ex FIFO, PEFP, Pull system etc.)
- Manage documentation as per laid down guidelines of Legal compliance and various audits
- Drive continuous improvements through various kaizen to address issues and improve efficiency & effectivity • Zero Downtime
- Timely closure of Audit Observations
- Zero Non-compliance to Processes
- Minimise Internal material handling damages
- Zero Accident
- Warehousing & Operations Planning
- Suggest design and utilisation of Shop warehouse for effective utilisation of space and material flow
Execute safe handling of material facilities
- Inventory management & obsolescence
- Execute receipt of Material, its Storage and Issue to Line
- Execute Engineering Change Management initiatives
- Perform Cycle Inventory as per statutory requirement and as per company guidelines
- Co-ordinate with SCM for minimising generation of non-moving / obsolescence materials • Minimise Material discrepancy
- Minimise Obsolescence
- Quality Management
- Ensure quality ok parts deliver to line
- Maximise Green packaging and damaged free parts and issue to line • No of returnable packaging
- Safety Management
- Adhere to the material handling guidelines
- Monitor and execute safety practices and its compliance • Zero Accident
- Cost Management
- Plan and propose annual Budget requirement of respective area.
- Monitor the cost of material handling damage and plan for minimisation of the internal material handling damages. • Budget v/s Actual
- Rejection Cost
Tata Motors Leadership Competencies
- Developing Self and Others – Recognizing continuous development is essential for success and taking steps to develop self and helping others to excel
- Leading Change – Recognizing the need for change, initiating and adapting to change
- Driving Execution – Translating strategy into action and execution
- Leading by Example – Encouraging and following ethical standards
- Motivating Self and Others – Inspiring teams and individuals
- Customer Centricity – Anticipating, understanding and focusing efforts on meeting the customer (stakeholders) needs or expectations