Schlumberger is Hiring | Product Engineer |
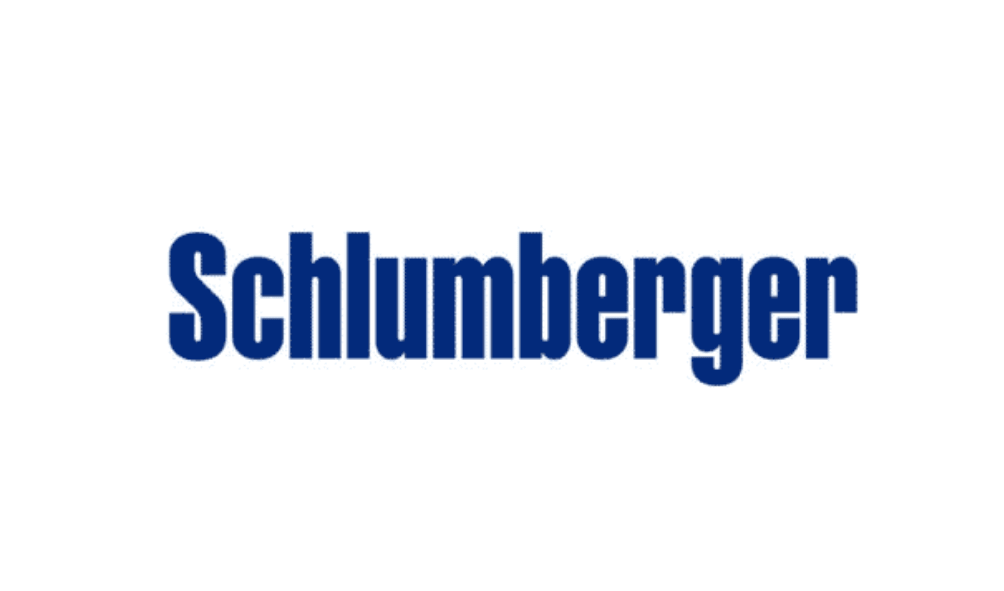
Position – Process Systems – Product Engineer
Company – Schlumberger
Location – Coimbatore, Tamil Nadu, IN
Job description
Job Summary
Perform process engineering calculations and address the process engineering design challenges. Keep abreast of industry codes, standards, regulations and guidelines. Meet or exceed project expectations in a timely manner within the budget limits. Co-ordination with intra / inter disciplinary team and provide the required deliverables as and when requested.
Defines the process to optimize product delivery throughout the facility, considering inputs from clients, products specifications, and cost of solution.
Size and define process equipment and utilities for O&G facilities during proposal and project execution
- Evaluate customer inquiries and specifications and select or recommend process or equipment designs for the application.
- Design equipment to match specifications or clearly define differences (clarifications or exceptions list) to customer.
- Develop “deliverables” for cost estimating, design engineering, and drafting.
- Lead the development and creation of all project drawings including P&ID’s, vessels, structural and piping. Ensure that all drawings match, and that any changes are picked up on all applicable drawings.
- Confirm compliance with the customer’s purchase order regarding the proposal technical and process requirements.
- Perform complex process simulations utilizing Cameron defined software.
- Create / review / comment on complex PFDs and P&IDs and perform P&ID walk-downs on fabricated equipment.
- Recommend, specify and requisition major buy-out equipment items such as heat exchangers and pumps.
- Perform equipment process design and mechanical design.
- Perform line sizing calculations.
- Select and locate level control equipment.
- Recommend control valve types and define PSV sizing basis.
- Generate Control Narrative and Control Philosophy documents.
- Develop cause and effect charts and participate in client HAZOP and internal HAZOP.
- Produce Installation, operating (Start-up and Shutdown) and Maintenance Instruction manuals, including lists for Consumables, Special Tools, Lubricants, and Utilities.
- Prepare instructions for Long Term Storage of equipment.
- Perform final review of Project Job Manuals.
- Develop equipment data sheets and estimate equipment weights.
- Provide technical support for trouble shooting
- Perform on-site start-up and / or trouble shooting
Minimum Job Qualifications
- Minimum Bachelor of Science degree in Chemical, Petroleum, or Mechanical Engineering, Experience required in the design and selection of process equipment for the Oil and Gas Industry
- 5 to 12 years of relevant experience (No. of years will vary based on product engineer level)
- Knowledge of national and international codes and standards for oil field process equipment design, shop fabrication procedures, inspection and NDE requirements, shipping preparation and terms, and field installation and start-up procedures.
- Competent in process equipment design and sizing.
- Experience / skill with multidiscipline project engineering functions
Preferred Qualifications
- Utilizes knowledge and skills as sound contributor. Organizes and manages multiple concurrent projects. Begins to lead small sized activities aligned with Cameron ETCL.
- Ability to size/review process equipment to meet design criteria.
- Ability to produce/review PFDs and P&IDs.
[su_button url=”https://xjobs.brassring.com/TGnewUI/Search/home/HomeWithPreLoad?PageType=JobDetails&partnerid=389&siteid=175&jobid=1505814#jobDetails=1505814_175″ target=”blank” size=”6″ center=”yes” radius=”0″ id=”Apply now”]Apply on Company Site[/su_button]