TATA Motors is Hiring | Multiple Openings |
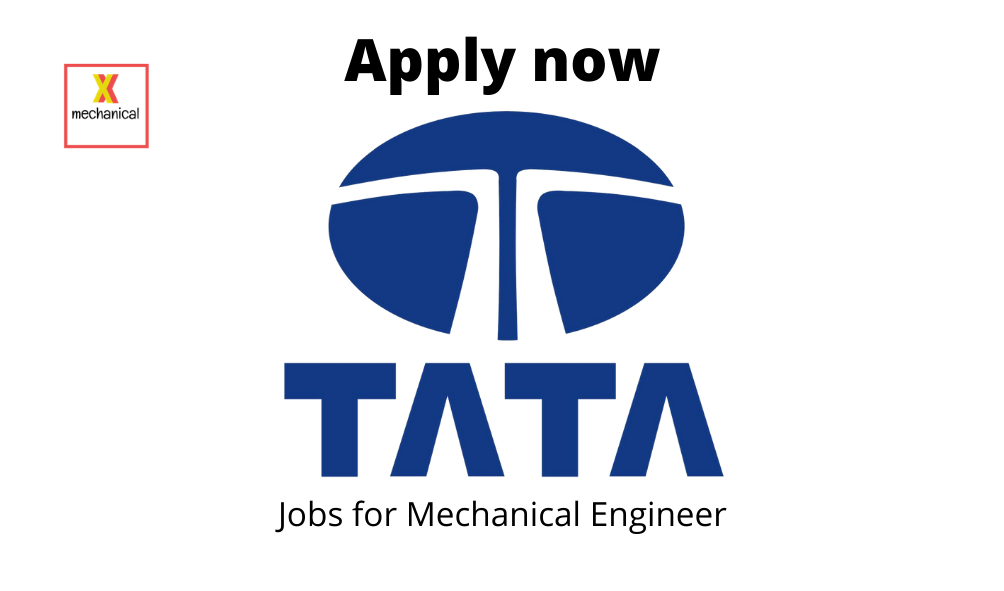
Position – SR. Manager, TCF MAINTENANCE
Company – TATA Motors
Location – Maharashtra, IN
Job description
Position Summary with Job Responsibilities.
Education – Bachelor of Engineering in Mechanical or Electrical
Work Experience – Min 3 Years of Experience
Preferred Industry – Auto Industry/ Auto Ancillary/ Manufacturing Industries
Tata Motors Leadership Competencies
- Developing Self and Others – Recognizing continuous development is essential for success and taking steps to develop self and help others to excel
- Leading Change – Recognizing the need for change, initiating and adapting to change
- Driving Execution – Translating strategy into action and execution
- Leading by Example – Encouraging and following ethical standards
- Motivating Self and Others – Inspiring teams and individuals
- Customer Centricity – Anticipating, understanding, and focusing efforts on meeting the customer (stakeholders) needs or expectations
Position – SR. MANAGER (L5) – DIE DESIGN”
Company – TATA Motors
Location – Maharashtra, IN
Job description
Position Summary with Job Responsibilities
Position Name Senior Manager, Project Execution Press Shop Position level L5
DEM position name Lead- Technical Services Press Shop PVBU DEM position level L4
FEM position name FEM position level
Purpose of the position
- Planning role which help in execution & implementation
- Study Part Manufacturability which includes Draw ability
- Installation and commissioning, Quality proving; Change management
- Selection for Equipment’s & capabilities, Vendors & capabilities; Facility/ equip planning; Investment planning & budgeting; Factory act; legal, environment & safety aspects; Asset management; TPM; Low cost automation, etc
Size
Financial Non-Financial
Finance basics Direct Reports:
RFQ preparations, Possible Vendors selections Indirect Reports:
Capex & Revenue Budget Volumes:
MS:
Education
Work Experience
Personal Profile
Education B.E/B. Tech. (Mechanical)
Skills/ Competencies
Behavioural (Tata Leadership Practices) Functional/Technical
- Customer Focus Knowledge of Sheet metal processes
- Dealing with Ambiguity Project management skills
- Drive for Results Knowledge of Press Shop equipment as well as facility related knowledge
Relevant Experience :
- About 3-4 years end to end Experience in Automobiles/ Others.
Key Responsibilities:
- Manufacturing Process Expertise
- Ability to provide consultation to vendors, other plants
- Can introduce innovative methods for break-through process performance
- Know latest trends and can explore advance mfg processes
- Can prepare process design manual
- % Adherence to Budget (Incurrence vs. Variance)
- Adherence to timelines & requirements
- % Savings (Y-o-Y) through improvements
- % Compliance
2. Lean techniques
- Lean mfg; line balancing; Buffer and flow management; layout planning; Standardization; Industrial engg, MOST; Logistics, JIT, kanban; etc
- Uptime in %
- % Availability of equipment services
- Operating Cost of services (Rs)
- MTBF/MTTR
3. Simultaneous Engineering of sheet metal parts / BIW Processes
- To Study Part Manufacturability which includes Draw ability, Cutting/Cutter Condition, Flanging Conditions etc.
- Part feasibility input to product designer thro’ ECR.
- Product Design via ease of manufacturing.
- To modify part with confirmation with design to aid reducing No. of strokes, thus process cost.
- Suggestions to provide PLP’s & MCP’s for part proving and fixturing purposes.
- Die life improvements
- Rs / car saving , GEN3 Process adherence ,
- Sheet Metal Panels Dies Development activities
- Monitoring Draw, Flange simulations on software like Auto-form & Hyper-form to optimize Draw ability, Blank Size, Quality of the part.
- Simulations for cracks, wrinkles, bead lines, blank sizes, spring-back, analysis and suggestions for improving the same.
- Die Design approval according to Specified Press Specifications.
- Die designs suiting to Automated line if required. Meeting all requirements of Automation line like Maximum SPM, Pass Height, Lift Stroke, Motion Curve, Interference Curves, Vacuum Cups placement and Windows etc.
- Pattern Checks, Casing Checks, Manufacturing Follow-ups -Method plan finalization
- -Yield improvements
- -PIST of final part
Tata Motors Leadership Competencies
- Customer Centricity – Anticipating, understanding and focusing efforts on meeting the customer (stakeholders) needs or expectations
- Developing Self and Others – Recognizing continuous development is essential for success and taking steps to develop self and helping others to excel
- Driving Execution – Translating strategy into action and execution
- Leading by Example – Encouraging and following ethical standards
- Leading Change – Recognizing the need for change, initiating and adapting to change
- Motivating Self and Others – Inspiring teams and individuals
Position – SR MANAGER – ADVANCED QUALITY
Company – TATA Motors
Location – Maharashtra, IN
Job description
Position Summary with Job Responsibilities
- This role is responsible to manage new part development with suppliers in order to facilitate launch of new product or meet the various changes needed in existing products.
Key Responsibility & Key Tasks
- Design Feasibility & Supplier Selection
- Analyse the part design received from Engineering for manufacturability of the part as Matched Pair team along with Engineering and Purchase
- Engage with supplier in early vehicle development phase to ensure quality and timely delivery of new parts (EVI – Early Vendor Involvement)
- Identify, and recommend potential suppliers after receiving SOR from engineering.
- Shortlist suppliers based on technical capabilities in the sourcing council by conducting technical review sign off (TRSO) along with Purchase, Engineering and FMQ.
- Conduct as a CFT member, Design Failure mode and Effect Analysis (DFMEA) review, in order to ensure that all past potential Design failures are captured in the current design
Part development planning
- Prepare a plan for every part (PFEP) under the vehicle build plan
- Prepare Advanced part quality plan (APQP) for every part to meet the timelines of vehicle build plan in partnership with supplier
- Study the part design and list CTQ parameters to ensure fitment and reliability of the part
- Design Validation plan sign off mentioning test start/ end date as per Engineering agreed specifications.
- Prepare part Manufacturing Planning at supplier end by creating Process Flow Diagram, Floor Plan Layout, PFMEA and RPN Reduction Plan, Facilities Preparation, Machinery & Equipment requirement, Tooling and Packaging Specifications
- Verify Tier 2 supplier Planning by validating their Tooling, Equipment, Production capacity, PPAP, Run @
- Rate verification
- Prepare Quality Plans which includes APQP Program Review frequency, Control Plans, Gauges / Checking
Fixtures, Operator and Gauge Instructions, Boundary Samples and TGR/TGW
Plan and verify that the team leaders, quality team members and operators are trained for production and quality of the part
Review in detail and assess readiness for Tooling Kick Off (TKO), Monitor tool development including risks associated
Part Development
- Obtain initial samples and take quality approval for the part from Quality Assurance team (IR/MR)
- Conduct 3 stage PPAP by Process Validation, Material Evaluation, Early Production Containment, 1st parts off serial tool, Matching / Dimensional validation, Capability Studies, Run @ Rate
- Drive Installation Quality Audit (IQA) along with production quality and supplier for proprietary and black box items.
- Conduct Vehicle level FTR (Fitment trail report ) sign off with required CFT members
- Sign off part submission warrant (PSW) to certify that the part has been developed as per required specifications and to meet the planned volume needs.
- Plan for Early production issue containment to ensure quality of early deliveries
- Monitor and prepare PPM report of the developed part for a fixed duration
- Tool management and Cost Reduction
- Identify VAVE opportunities and Implement to achieve cost reduction targets
- Manage tool capitalisation and process pay outs
- Conduct the tool audits, get the identified issues closed and submit audit/closure reports
- Supplier Management
Education
- BE/B Tech
Work Experience
- 3- 9 years
Tata Motors Leadership Competencies
- Customer Centricity – Anticipating, understanding and focusing efforts on meeting the customer (stakeholders) needs or expectations
- Developing Self and Others – Recognizing continuous development is essential for success and taking steps to develop self and helping others to excel
- Driving Execution – Translating strategy into action and execution
- Leading by Example – Encouraging and following ethical standards
- Leading Change – Recognizing the need for change, initiating and adapting to change
- Motivating Self and Others – Inspiring teams and individuals
Position – SENIOR MANAGER (L5) – FMQ ENGINE & AFTER TREATMENT SYSTEM
Company – TATA Motors
Location – Maharshtra, IN
Job description
Position Summary with Job Responsibilities
COC FMQ for Engine & After treatment system
Root cause analysis of field failures in existing products e.g. 7D, SPS, Failure data analysis, DMAIC expert
- Preparation of QIB from existing warranty, Inhouse, thermal incidences, BITS & CCT issues. Driving for closure of all issues through NPI projects before the product is reached DR5 gate
- DMU review for DVLO, Tolerance stack up, Fire path analysis
- Participation in DFMEA, CTQ execution, SOR,TRSO, IQA and PPAP
- Leading DMU activity & action planning for the closure of the issues arising thereby.
- Field visits for root cause and action planning for the failures ( if any) in the newly launched vehicle.
- Achieve IPTV & EPV (3/6/12/24 MIS) targets of the new launches while working on Cimple projects.
Education
- B.E / B. Tech / M.E / M. Tech. (Mechanical / Automobile)
Bachelor of Engineering in Production
Work Experience
- work experience (in years): 4-7 years
- Preferably on design & development, APQP/PPAP knowledge would be added advantage, Operations Quality,
- Vendor development
Position – SENIOR MANAGER (L5) – ENGINE ASSEMBLY
Company – TATA Motors
Location: Maharshtra, IN
Job description
Position Summary with Job Responsibilities
- Should be able to manage production in shift
- Controlling Tool management for calibration as well as new development/IDM management
- New product Introduction & related documentation
- Coordination for Process/IATF/ZDS/other audits & closure of NCs
- Meeting Facility requirement for ensuring smooth production
- Understanding DWM/MP/CP as well as analyzing data
- Thorough understanding of RCA/ICA/PCA/Problem solving tools/PSR
- Idea generation & Implementation for VA/VE, QMSG,TCS,VFW
- Updation of documentation after any modification with reference to SQPDCME
Education
- BE/B Tech
Work Experience
- 5+yrs
Tata Motors Leadership Competencies
- Customer Centricity – Anticipating, understanding and focusing efforts on meeting the customer (stakeholders) needs or expectations
- Developing Self and Others – Recognizing continuous development is essential for success and taking steps to develop self and helping others to excel
- Driving Execution – Translating strategy into action and execution
- Leading by Example – Encouraging and following ethical standards
- Leading Change – Recognizing the need for change, initiating and adapting to change
- Motivating Self and Others – Inspiring teams and individuals