Molex is Hiring | Quality Engineer |
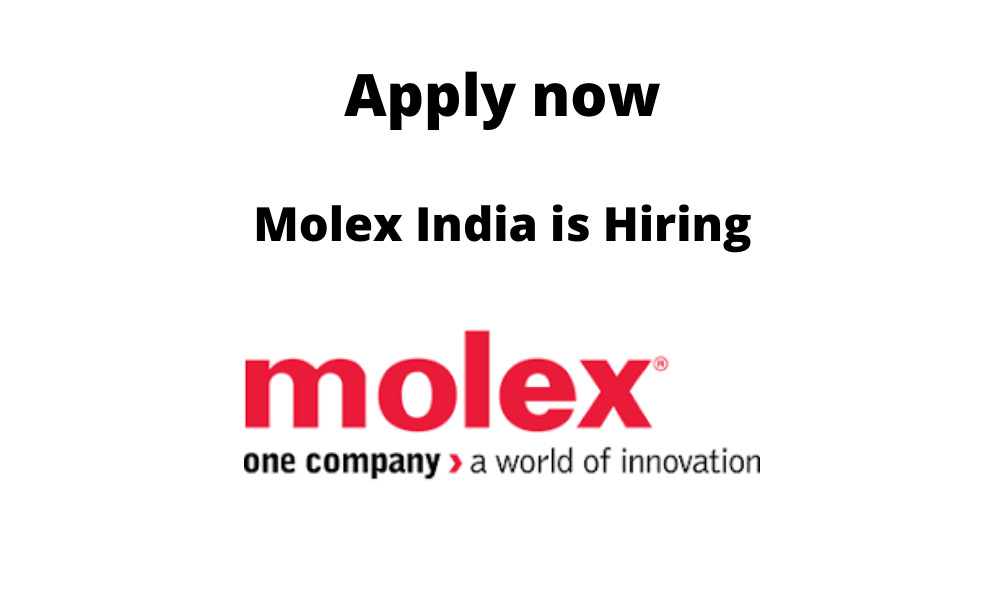
Position – Supplier Quality Engineer
Company – Molex
Location – Bengaluru, Karnataka, IN
Job description
PRIMARY PURPOSE: | Work as a design center Supplier Quality Engineer for Global projects.Work closely with AQP managers and Engineers at different design centers to execute L1 and L2 qualifications accurately and on-time during the appropriate phase.Create components qualification plans and follow up for the PPAP documents from suppliers. These deliverables help manage and mitigate project risk to ensure a Flawless Product Launch that meets customers Cost, Quality, Delivery requirements. |
DUTIES & RESPONSIBILITIES:
1. | Work independently as a design center Supplier Quality Engineer for Global projects (NPD/MOD/SPO&TSP) by executing all components qualifications according to NPI direct AQP Deliverables. Component qualification plan development:Ensures the qualifications plans for new components and modified components are created and supplier PPAP documents are tracked on timely manner. Provide regular updates to the responsible design center AQP Managers. |
2. | Store all PPAP documents on Project Share Point site on designated folders within the planned date according to project timeline and update the phase deliverable checklist regularly. |
3. | Be an expert and have good product knowledge of different design centers (Cable assemblies/Cage and connectors). Maintains and updates the Internal knowledge database. |
4. | Create a tool list (tracking document) for the RPM purchased parts |
5. | Qualification Plan: Complete the qualification plan – Signers: plant AQP and DAQP, PDE, MIE – send and review with suppliers and Update qualification plan for any design changes while still in Phase 7 and requalify |
6. | Work directly and push suppliers for FAI, CS and PPAP in a timely manner |
7. | Get samples of parts for FAI and submit to India/other measurement lab for Supplier Audit |
8. | Push product team for disposition of FAI and CS; upload all dispositioned reports to Midas per current NPI-D procedures |
9. | Tooling Fix: Based on the disposition from AQP, PDE and MIE communicate to supplier if there is a need to fix/correct/improve the tooling – get an ECD for the same and keep informed project team and continuously follow up with supplier based on the dates they have provided. |
10. | Production support before tooling fix:if the tooling fix takes more time and causes a line down situation – coordinate with Sourcing team/PJM/Plant to make sure we get enough stock before supplier take down the tool for correction/repair/improvement. |
11. | Internal Deviations: Create internal deviations on SAP to make sure that production line gets material before completing FAI whenever its necessary based on the agreement with PDE and cross functional team |
12. | PPAP review– Review all the PPAP documents received from supplier according to PPAP review checklist, make sure all the documents provided according to component qualification plan |
13. | Incoming Inspection: Work with plant SQE to prepare documentation needed for incoming inspection per plant process |
14. | Gauge and Fixture: Facilitate design and procurement of any gages or fixtures needed at incoming inspection |
15. | Measurement issues: Resolve measurement issues between supplier, plant, and India measurement lab |
16. | Supplier PFMEA: Review supplier PFMEA according to PPAP checklist and upload it to specific folder on Stature. |
17. | AQP Deliverables/Share point tasks: Support AQP deliverables and work on share point tasks (CPMP, Inspection checklists, Lessons Learned, inspections instruction, etc..) |
18. | MBM & Quality Systems:Understand & practice the KOCH MBM philosophy & guiding principles, International Standards Organization (ISO) by following stated policies and procedures. |
SCOPE: | Supports design center/plant AQPs at multiple sites to ensure qualification plan and supplier PPAP documents are tracked on timely manner and maintained per latest drawing revision for all purchases components for all CSBU new products. Works as an independent SQE to complete all supplier PPAP deliverables. Accountable to the design center AQP and AQP manager at applicable sites. |
EDUCATION:
REQUIRED: | BS or master’s degree in Mechanical/Industrial Engineering or another related field |
PREFERRED: | Training in Advance Quality Planning Tools like DFMEA, PFMEA, PFD, CP, training on PPAP. |
WORK EXPERIENCE:
REQUIRED: | 4 – 6 years’ experience in Quality Engineering or related engineering field |
PREFERRED: | 4+ years’ experience in Quality engineering in a new-product introduction environment as an SQE |
SKILLS & ABILITIES:
REQUIRED: | Excellent communication is a must, Listening skills and a quick learnerStrong knowledge on APQP and PPAP deliverables.Fair idea on PMS (product design and development – mass production)Strong organizational skill to anticipate, plan, organize and self-monitor workloadGood interpersonal skills for effective leadership and team facilitationSolid Knowledge & understanding of Engineering drawings, metrology, and GD&T4+ years knowledge of statistics – experience using Minitab or other software4+ years using MS Office (Excel, Word, Power Point)Able to travel (domestic and international) 5% – 10% |
PREFERRED: | Working knowledge of electronic assembly, testing, molding, stamping, plating, and assembly processesQuality System (ISO 9001 or TS 16949) and Supplier Auditing experience, Gage and Fixture designKnowing Chinese would be an added advantage“Koch is proud to be an equal opportunity workplace” |
[su_button url=”https://jobs.kochcareers.com/jobs/6956977-supplier-quality-engineer?tm_company=12614&tm_event=view&tm_job=KOCH-INFOR-11199″ target=”blank” size=”6″ center=”yes” radius=”0″ id=”Apply now”]Apply on Company Site[/su_button]