Kone is hiring | Engineer – Production |
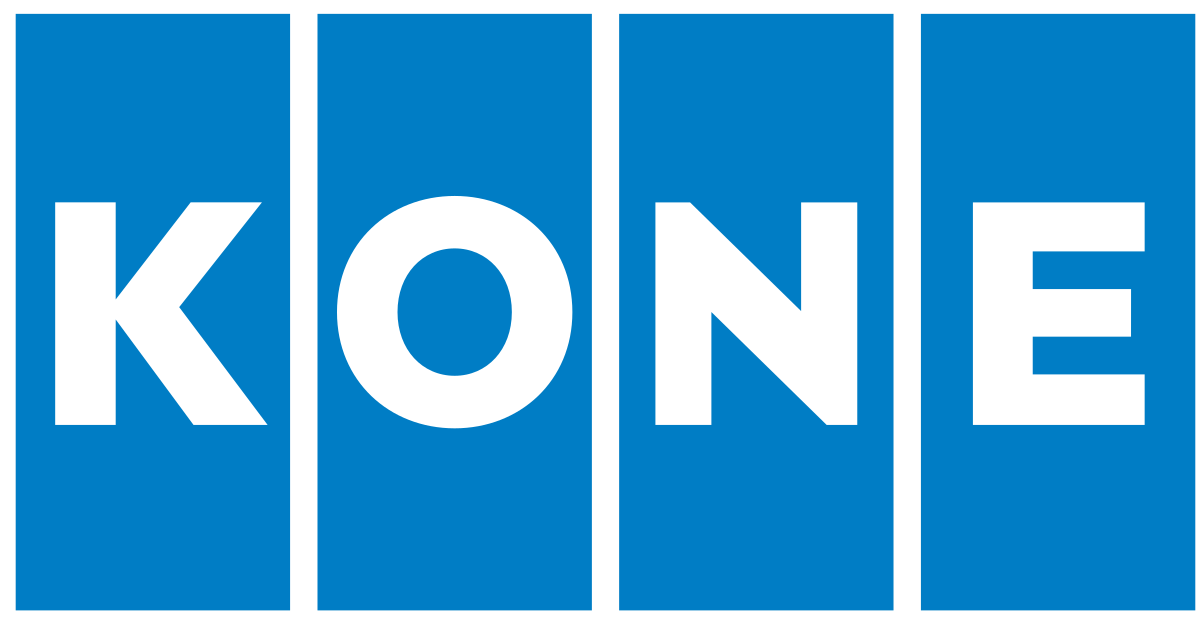
Position – Engineer – Production
Company – Kone
Location – Chennai, Tamil Nadu, IN
Job description
Did you know KONE moves over one billion people every day? In 2019, we had annual net sales of EUR 10 billion. We employ over 60,000 driven professionals in over 60 countries worldwide joined together by a shared vision. As a global leader in the elevator and escalator industry, it is our mission to improve the flow of urban life.
Job Title – Engineer – Production
Major part of the Production Engineer’s role is figuring out how to manufacture parts or products with maximum efficiency.
Mathematics and Engineering are vital skills for Production Engineers. That includes statistics, design, computer skills and knowledge of production systems. The learning doesn’t stop, as you’ll have to keep up with technological changes and improvements that affect your field. Because the job involves so much interaction, you’ll need good people skills as well.
Are you the one?
- Degree in Mechanical Engineering or related field.
- Minimum 2 to 3 years of experience in punching, laser, and bending machines.
- Experience working in Manufacturing industry
- Good interpersonal and communication skills.
- Excellent time management skills.
- Ability to multitask.
- Knowledge of health and safety regulations.
What will you be doing?
Basic Responsibilities:
- Plan and coordinate Production Engineering processes on daily basis to produce High quality products.
- Develop process improvements to effectively utilize equipment and materials to maximize production.
- Develop operational strategies to achieve production and financial objectives Including Consumable and Packaging.
- Identify unsafe operations and practices and report the same to Manager immediately.
- Establish safety procedures and environmental regulations for employees.
- Provide engineering support for production and maintenance activities to ensure maximum production.
- Perform engineering analysis to reduce downtime and outages.
- Evaluate current production activities and make recommendations for improvements.
- Implement cost reduction initiatives while maintaining high quality standards.
- Develop operating instructions and equipment specifications for production activities.
- Provides training and guidance to team members to accomplish production goals.
- Stay current with product specifications, engineering technology and production processes.
- Develop best practices to improve production capacity, quality, and reliability.
- Investigate problems, analyze root causes, and derive resolutions.
- Aid in budget preparation and monitor expenses of Packing and Consumables.
Key Responsibilities:
- Prepare a Production Plan report based on WIP Report with specification details and share it to the work center.
- Monitoring of Pre-treatment and Powder coating process.
- CAPA on action plans (Internal as well as External).
- Manpower allocation based on workload to the Work center.
- Hourly Production Report Monitoring and reporting to the Manager.
- Daily Production Plan Execution and Completion and reporting to the Manger.
- Daily WIP Review Completion and reporting to the Manager.
- Daily Production Efficiency Monitoring and reporting to the Manager.
- Required Consumable Material request order to Material Management Team against Production Order.
- Required Tools order to MFS Team.
- Quality Feedback (QFB) Analysis.
- QFB Material to be ensured for on-time delivery.
- Spare order Material to be ensured for on-time delivery.
- Rejection Material offers to Quality and get the SR Approval.
- Productivity Improvement Action Plan.
- Daily Record Non-Value-added activity from each work center.
- Daily Record Quality Issues from each work center.
- Daily Record Break down time Issue from each work center.
- Daily Record Engineering Issues like BOM errors, DRG Issues, DXF issues, and Clarification from each work center.
- Ensure all Systems are available with good working conditions from the Work center like PC, scanner, Printer, and network availability.
- Maintain 5S in all WorkCentre,
- Ensure Safety and Environmental Aspects in all work centers including PPES.
- Execution of Operator Matrix Development Plan.
- MIS Report Preparation.
- Kaizen Report Preparation.
- Near Miss Reporting to the Safety department.
- Implement Development activities like conveyors, New fixturess, and New Processes along with MFS Team.
- Execution of Annual Physical Stock Verification.
- Weekly Toolbox Meetings are Conducted for Safety, Quality, and Management Communication.
What do we offer?
- Career progression and opportunities within a global organization
- Total reward elements that engage and motivate our employees and help us make KONE a great place to work
- Comprehensive learning and development programs covering a wide range of professional skills
- You are surrounded by fun colleagues and a lively working environment within the Business Services team and KONE Front Line. The best part is all leaders are great and open-minded
Click on apply if you have a passion for meeting up with people and a desire to make an impact in the elevator and escalator industry.
At KONE, we are focused on creating an innovative and collaborative working culture where we value the contribution of each individual. Employee engagement is a key focus area for us and we encourage participation and the sharing of information and ideas. Sustainability is an integral part of our culture and daily practice. We follow ethical business practices and we seek to develop a culture of working together where co-workers trust and respect each other and good performance is recognized. In being a great place to work, we are proud to offer a range of experiences and opportunities that will help you to achieve your career and personal goals and enable you to live a healthy and balanced life.
Read more on
www.kone.com/careers