Johnson & Johnson is hiring | Graduate Engineer Trainee | Graduate in Mechanical or Electrical Engineering |
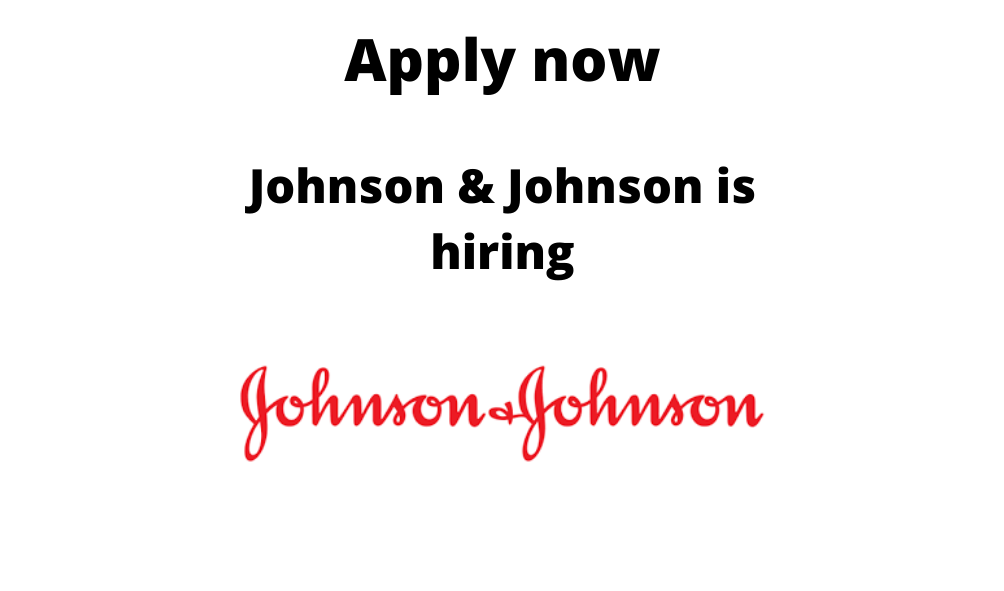
Position – Graduate Engineer Trainee
Johnson & Johnson Family of Companies
Location – Mumbai, Maharashtra
Job description
- Reliability Engineer will take the ownership of operational management and delivery of Facilities Reliability Services delivered within his/her location. This includes the management of customer interface within the designated area of an estate; ensuring efficient service delivery of day-to-day running of the sites, and provision of a consistent strong link with internal customers, guaranteeing appropriate and responsive reaction to address concerns regarding India and also support to the SEA E&PS team.
- This is an active and visible role requiring excellent asset management, reliability management skills. Working as a part of the team within the business, the Facility Management (FM) is expected to positively contribute to the performance of the business by engendering a culture of customer relationship & proactive approach.
- To determine Maintenance Strategies and Approaches, Failure Process, Characteristics, Causes and Types
- To determine Asset Criticality, Risk Based Approaches, FMECA, RCM, REM of assets, Predictive Maintenance.
- To apply engineering knowledge and specialist techniques to prevent or to reduce the likelihood or frequency of failures
- To identify and correct the root causes of failures that do occur
- To determine ways of coping with failures that do occur, if their causes have not been corrected
- To apply methods for estimating the likely reliability of new designs and analysis of reliability data
- To manage the project and commissioning planning with effective & efficient Asset management and optimization.
- LRFP- long Range financial planning.
- Contributing in Opex management.
- Generation of capital business plan.
- Exclusive focus of FCI, facility condition, road map generations.
- Execution of New Asset / Infra installation.
- Asset data management.
- To lead the maintenance team in maintenance best practices and managed reliability programs.
- To implement equipment upgrades via the MOC (Management of Change) process. Acting as a liaison between intra dept. Maintenance and Operations to schedule work for major plants shutdown activities and large capital projects.
- To manage the design, procurement, and construction of capital projects in accordance with EHS&S requirements.
- Contributing ideas to lean manufacturing and process improvement events.
- Developing and Implementing Risk Based Maintenance Plans, Work Control, Planning and Scheduling of maintenance task.
- Overall Equipment Effectiveness, Root Cause Analysis and Maintenance
- Lower cost of repairs –fewer spares and less time
- Fewer surprise breakdowns and risks to supplying customers
- Less catch-up time on overtime
- Better equipment reliability from Risk Based Maintenance
- Release of equipment capacity –able to delay future investment needs
- Maintenance involvement in equipment selection –lower life cycle costs
- More sensitive operation of equipment
- Better man-power utilization –avoiding delays
- Fewer rejects, less waste, more yield from materials
- 1st level maintenance –ownership of equipment
- Technicians released to do diagnostic work –longer term.
- Providing Similar Support to the required SEA E&PS team.
- Asset Reliability & management.
- Failure mode and effects analysis (FMEA)
- Reliability hazard analysis
- Dynamic reliability block-diagram analysis
- Fault tree analysis
- Root cause analysis
- Avoidance of single point of failure (SPOF)
- Functional analysis and functional failure analysis (e.g., function FMEA, FHA or FFA)
- Testability analysis
- Human error analysis
- Operational hazard analysis
- Preventative/Planned Maintenance Optimization (PMO)
- Manual screening.
- CMMS knowledge for problem solving
- Electrical testing equipment
- Author and understand technical reports
- Reliability Availability and Maintainability (RAM) Program knowledge
- Solid history of effective testing and improvement
- Support in Facilities MIS & Dashboards – Reliability
- Compliance – Regulatory, Quality & EHS&S (Reliability part)
- Facilities Commercial Activities
- Excellent interpersonal skills
- Team management and leadership
- Work with individual site team members to develop consistent, reliable practices to deliver high quality, productive, safe workplace environments.
- Provide change management leadership to implement Facilities strategies and initiatives at the site on behalf of Site facilities lead.
- Establish a high performance and continuous improvement culture driven by key performance metrics, benchmarking and sharing of best practices.
Qualifications
- Engineering Graduate in Mechanical or Electrical Engineering including sound knowledge of asset management
- Good working knowledge of one functional core area.