Collins Aerospace is Hiring | Assistant Manager |
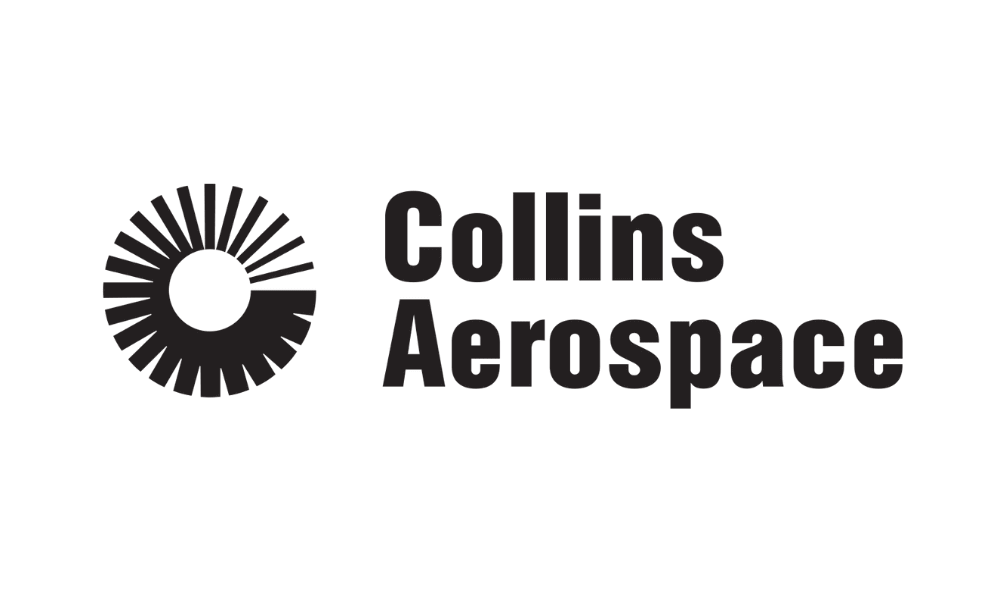
Position – Assistant Manager – Industrial Engineering
Company – Collins Aerospace
Location – Bengaluru, Karnataka, IN
Job description
This position is accountable for providing both technical and Industrial Engineering/process leadership mainly in the areas related to applications; Assembly, electrical/electronics; mechanical; manufacturing; quality; safety, health & environmental; or software. Provide recommendations for changes to working methods or operation sequences that will minimize risks, costs, and wastage; increase yields and productivity; and improve the quality and consistency of final products.
1. Leads specification, design, analysis and development of New Products/processes, Industrial projects & Factory Layouts based on Industrial Standards. Creates layout in AutoCAD and converts into physical layouts.
2. Evaluates and validates design alternatives to create optimum process designs.
3. Leads the teams of engineers and technicians through industrialization activities for set up and change manufacturing process.
4. Participates in strategic planning as a member from engineering and technology development effort.
5. Acts as a technical consultant on process and methods engineers or for anyone who needs the service related with industrial knowledge.
6. Coach and mentor less experienced engineers.
7. Develop Standard Work/Triplets for processes based on Best Available Techniques and Methods.
8. Conduct Time and Method Study based on MTM/MOST techniques.
Areas of Responsibilities
- Industrial Efficiency through continual improvements
Identify process related issues through Tier meetings; study the turn backs/ down time trends. Define problem areas and identify root cause. Propose solutions to eliminate the root cause; implement and evaluate effectiveness. Update process documents by incorporating the changes. Continually look for ways and means of improving productivity. Implement idea schemes within defined area of work.
- Launching new products
Receive the new projects documents from industrial team for all new projects. Study, evaluate and identify improvement points if any; Incorporate them before launch of the New products and transitions.
- Qualification of Test Benches/Stations:
Study the basic machine design. Study performance of the machine by producing a minimum lot on a particular machine. Validate the products produced with the support of quality. Study the time taken for production; Qualify the machine based on the results of the above study.
- Support Product Qualifications & FAI’s
Conduct Line short run on the qualified machines to find the areas of improvements if any. Based on identified areas of improvement take corrective / preventive action, Implement the same as part of the system. Confirm the process Capability of machines/lines and make them available for production
- Troubleshooting / Problem Solving on a daily basis
On a daily basis get to know quality issues, inadvertent breakdowns in the lines. Understand the problem and suggest alternative solution to immediately address the problem and regain production. Discuss with other product lines if required to identify and implement possible solutions; Work towards providing long term solutions to arrest the reoccurrence of the problem.
- Process capabilities
Monitor and measure process capabilities periodically. Take action based on deviations from the quality, production, and supply chain ; Analyze the issues and improve the process; Take trials to revalidate the process and re-establish the process documents
- Capacity planning and manpower forecasting :
Receive long term Demand forecast from VPS for Long term planning; Review capacity quarter-wise and take action to ensure capacity availability as per requirements; Check the capacity for both in-house and subcontractor capacities. Identify bottlenecks if any and work on removing the bottlenecks; Organize and implement the production facilities required for new capacity or for improved quality. Estimate manpower requirements for new capacity and inform HR for manpower planning. Ensure implementation of increased capacity on time such that, market demands are met as per requirements.
- Implement ECNs (Engineering change notes)
Receive ECNs from the technical department; Study and find out implications on the existing process; Change the process to suit the ECN requirements; Update the relevant database and documents at the workstation. Call for prequalification of the processes as required. Train the concerned operators / supervisors to implement the changes; Manage change effectively.
- Implementing ACE
Support ACE Operating System in Operations and support functions with reference to lean procedures; Ensure optimization of production floor layouts. Understand Layout, Linkage and flow and ensure implementation of same; Organize ergonomics and safety. Be Aware of TPM and make changes in process in line with TPM requirements; Ensure appropriate Methodology and optimization of Material providing and handling. Implement Poke yoke and FMEA where ever required.
- Technology transfer from Projects
Learn the products and process from the projects team. Participate in the implementation, validation and qualification of the processes. Take charge of all technology transfer documents including drawings, test methods SOPs. Train the production team in implementation of the processes; Prepare and provide commission reports to the projects, maintenance and finance team.
- Handle Transfer Projects
Receive requirements from mother plant, define schedule for the projects; brief the projects with internal department like procurement, technical logistics and production. Prepare samples and get validated. Support in preparation of product costing and logistics feasibility. Validate the process variability.
- Prepare & Update SOP’s & Triplets
Adhere to the changes and improvement made and align SOP’s and triplets in line with the same. Re-align Standard Work periodically and ensure training to the production team to implement changes.
- Annual Budget planning
Make budget provision for equipment’s, consumables, tools and seek approval for the same. Follow the budget and ensure expenses made within budget limits
[su_button url=”https://careers.rtx.com/global/en/job/01503107/Assistant-Manager-Industrial-Engineering”]Button text[/su_button]
Collins Aerospace, a Raytheon Technologies company, is a leader in technologically advanced and intelligent solutions for the global aerospace and defense industry. Collins Aerospace has the capabilities, comprehensive portfolio and expertise to solve customers’ toughest challenges and to meet the demands of a rapidly evolving global market.
The next chapter of our future as an aerospace company is here, and we are excited about what this means for our employees and customers! Get onboard the Collins Aerospace Operations team and play a part in managing our innovative products from inception to delivery. The Operations team continues to grow and aims to strengthen the connection of Manufacturing Operations, Supply Chain and Environment, Health & Safety (EH&S) across Collins Aerospace. In this dynamic environment, you will have the opportunity to network across our businesses and functions, all while improving the productivity, quality and efficiency of our operations worldwide.
Collins Aerospace Diversity & Inclusion Statement:
Diversity drives innovation; inclusion drives success. We believe a multitude of approaches and ideas enable us to deliver the best results for our workforce, workplace, and customers. We are committed to fostering a culture where all employees can share their passions and ideas so we can tackle the toughest challenges in our industry and pave new paths to limitless possibility.
WE ARE REDEFINING AEROSPACE.
Some of our competitive benefits package includes:
Benefits package includes:
- Transportation facility.
- Meal coupons
- Group Term Life Insurance.
- Group Health Insurance.
- Group Personal Accident Insurance.
- Entitled for 22 days of vacation and 7 days of contingency leave annually.
- Employee scholar programme.
- Work life balance.
- Car lease programme.
- National Pension Scheme
- LTA
- Fuel & Maintenance /Driver wages
- Meal vouchers
Nothing matters more to Collins Aerospace than our strong ethical and safety commitments. As such, all India positions require a background check, which may include a drug screen.
Note:
- Background check and drug screen required (every external new hire in the India)
- Drug Screen only performed for Operations Positions
At Collins, the paths we pave together lead to limitless possibility. And the bonds we form – with our customers and with each other – propel us all higher, again and again.
Apply now and be part of the team that’s redefining aerospace, every day.