BASF is Hiring | Executive |
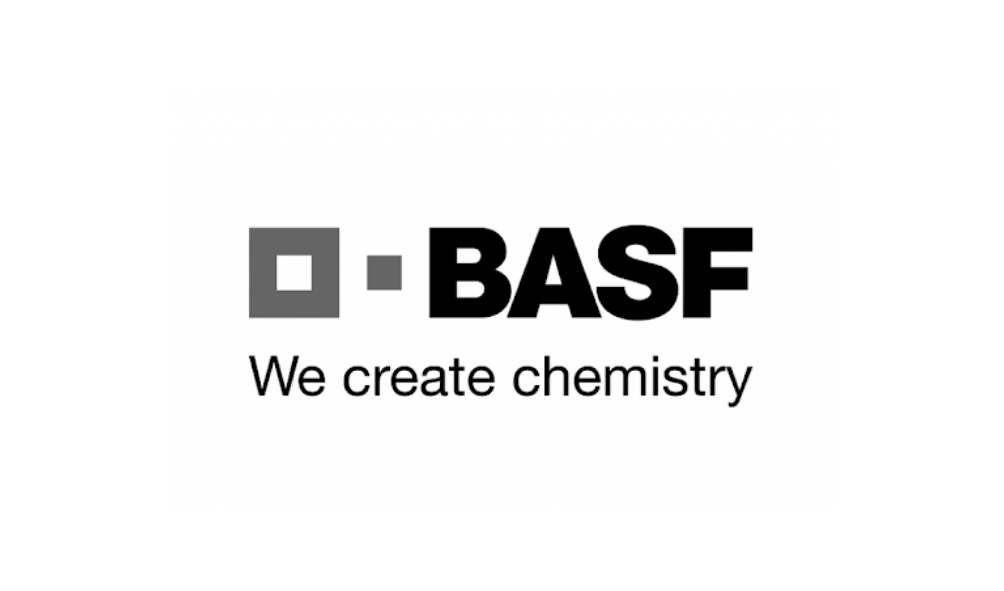
Position – Executive – Maintenance
Company – BASF
Location – Dahej, Gujarat, IN
Job description
We are a leading chemical company, with the best teams developing intelligent solutions for our customers and for a sustainable future. Our success as a company relies on the engagement of our employees. We encourage our employees to develop their strengths, and we recognize their achievements. For you, this means a wide variety of job roles, and exciting opportunities for learning and career development.
Description
- Objectives of the Position
- Why does this position exist? With what permanent objectives?
- Ensure plant and equipment reliability
- Ensure break down and preventive maintenance with cost and quality.
- Adhere to EHS requirement while maintenance work
- Main Areas of Responsibilities and Key Activities
General:
The role of the Maintenance Planner/Scheduler is to optimize expenditures and technician productivity through robust planning methods that support excellent scheduling and ensure safe and reliable plant operation. The Planner/Scheduler works jointly with maintenance teams to obtain an optimized total cost of materials and services, within specification requirements that support safe work practices and plant safety and operational objectives.
- The planner/scheduler is responsible for providing data to support maintenance KPIs.
- The Maintenance Planner/scheduler will be part of the site maintenance team and will be reporting to the Engineering Head.
- The Planner/scheduler’s primary responsibility is to review notifications, create maintenance orders, plan labor and material required to execute the order, scheduling, requisition of materials, maintenance order management, and SAP Database maintenance.
- This requires a working knowledge of SAP PM and a functional understanding of maintenance craft skills, tools, and equipment in the areas of responsibility.
Key Responsibility:
- Thorough working knowledge of SAP PM module.
- To screen all notifications to see that the notification accurately defines the scope of work, meets the criteria for the assigned priority, and is a valid request for work to be performed by maintenance personnel and financed by the applicable maintenance expense budget (Gatekeeping)
- To Convert notifications into maintenance work orders (WO) and creates a maintenance work plan. As needed, the planner/scheduler secures additional information prior to converting the notification into a maintenance order.
- Review the cost estimate with the applicable Maintenance Executive before proceeding with releasing the order, as required.
- Create detailed job plans for all WOs in the area of responsibility, except emergency WOs, via SAP. Detailed job plans could include – field walk down or evaluation; manpower estimates by craft or contractor to support scheduling and note any applicable safety regulations/concerns.
- Support maintaining SAP database. This includes data input for functional locations, equipment, bills of material, reusable job plans for repetitive jobs, predictive/preventive maintenance task list, equipment items, and maintenance plans.
- Provide materials through material reservations from warehouse stock for maintenance work.
- Maintain Preventive/Predictive Maintenance tasks/work orders via SAP to be used in the scheduling process.
- Create and maintain a database of planned ready-to-work WOs to be used in the daily/weekly or Turnaround (TAR) scheduling processes. This includes reporting accurate resource data to the maintenance team to support scheduling resource-leveling. Coordinate WO prioritization with Maintenance and Operations
- Create and publish weekly and daily schedules
- Attend daily update meetings with Maintenance executives to revise/finalize the next day’s or week’s work schedule.
- Provide input to the planning/scheduling KPIs and provide services to help meet KPI targets.
- Collaborate with maintenance, operations, and contractors; facilitate expedition of materials and services for work as per planning.
- Perform special duties as assigned by the Engineering Head that is applicable to the maintenance work processes.
- Following the execution of the work, certain critical information is recorded for future reference including correction of any parts related data, identification of the failure code for the work involved, update any reusable job plans as needed, the capture of any data specific to the job and included in the SAP record, Technical closure (TECO) of the WO.
- Handling of Contractor bill management system.
- Development of subordinates by identifying training needs and providing good working culture.
- Planning scheduling of maintenance activity as per ISO/IATF system.
RCMS Responsibility:
Executives are responsible to their Reporting Manager for the implementation of the EHS Policy and RC. Their particular Responsibilities and Accountabilities are to…
- Set an example of safe working.
- Ensure that employees and contractors are communicated about RC requirements.
- Assess employee safety performance and arrange any additional training requirements, if required.
- Ensure that all RC rules, procedures, regulations, and safe working practices are understood and adhered to by all employees and contractors.
- Ensure that tools and equipment are used for their intended purpose, properly maintained, and hazard-free.
- Inspect the workplace on a routine basis for potential hazards and take appropriate action to eliminate them.
- Promote and enhance engagements by regular Safety talk, Training to Employees, Contractors.
- Performs the role as defined in On-site Emergency Plan to mitigate emergencies.
Job Requirements (minimum requirement to carry out the work)
- Education – B.E. (Mechanical)
- Working Experience – 5-7 yrs
Technical & Professional Knowledge
- SAP PM module, Knowledge of maintenance activity for Chemical Industries, 5S, Safety Systems, Good Engineering Practices
[su_button url=”https://basf.jobs/dark_blue_AP/job/Dahej-Executive-Maintenance-392130/672068401/” target=”blank” size=”6″ center=”yes” radius=”0″ id=”Apply now”]Apply on Company Site[/su_button]